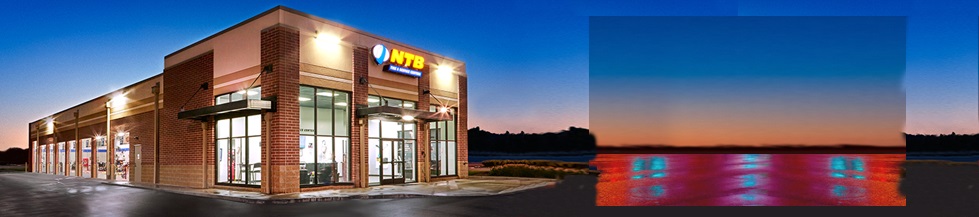
SHOP for TIRES
The Evolution of the Tire 1920s to the Present

Many of the major developments to tire technology took place longer ago than most people think. The vulcanization process, the pneumatic inner tube, the mountable rim, even the grooves cut to improve traction—all were introduced well before the 1920s. Still, the evolution of the modern tire is an interesting tale.
Let's start with a quick overview of how a modern automobile tire is made.
Tires are made up of several different materials. Natural rubber comes from the sap of the rubber tree, and comprises roughly thirty to forty percent of the rubber in the modern tire. Synthetic rubber is derived from petroleum byproducts and has roughly twenty different chemical makeups, each of which has specific properties and advantages that are selected from for particular tire needs.
Carbon black is a pigment derived from the incomplete combustion of natural gas or crude oil in a limited-oxygen environment. It is a fine soot stored in giant silos at tire plants, and is what gives automobile tires their characteristic deep black color, while providing a good deal of durability and ultraviolet resistance.
Sulfur is added to the rubber mixture to facilitate the vulcanization process. Before this process was discovered by Charles Goodyear - yes, the company was named after him - rubber was very sensitive to external temperature fluctuations. It would be soft and tacky when hot, rigid and brittle when cold. The introduction of white lead and sulfur to rubber (when they were left on a hot stove together) made a dramatic chemical change: Now the rubber was basically impervious to environmental changes, remained flexible, and revolutionized several industries.
Other chemicals are introduced to the rubber during the manufacturing process; some to ensure the tire remains flexible, some to protect from ultraviolet rays, some to ensure strength under load. Different tire needs require different specifications, so a racing tire will need a very different chemical makeup than the family sedan's, while the sedan may have different tires awaiting it for various seasonal requirements.
Even the portions of a tire can be composed of different rubbers to perform different jobs; the sidewall is different from the tread and so requires a different chemical outlook. Modern factories have computers dedicated to maintaining the recipes for these mixtures and can change up the compositions at a second's notice.
That's just the rubber. Modern tires are the product of an evolution in design that we will be getting to, thank you for reminding us, so there are several other materials that help make them up, including steel and fabrics. Steel wire makes the bead, the portion of the tire that affixes it onto the rim of the wheel, while cotton fibers cross at a different angle to the tire's tread in order to strengthen it and make it less susceptible to shredding.

This is to illustrate the shredding part, not the strengthening part, just to be clear.
Originally, the cotton fibers were placed at an alternating 55-degree angle relative to the tread, making what are known as “bias-ply” tires (from the plies, or rubber-coated threads, being laid at a bias, or angle). In 1948, an improved version of this approach was developed, with stronger threads of nylon or polyester, laid at a 90-degree angle to the tread. This “radial” version had a number of advantages over the bias-ply, but, as we shall see, was not immediately adopted everywhere.
The steel wires, introduced in the 1930s, are what enables the tire to hold fast to the rim of the wheel. They are embedded in a rubber sheath that is fused to the rest of the tire during the manufacturing process.
Speaking of which: The rubber, after being mixed, is squeezed through giant rollers into large, flat sheets that are separated depending on what future use they will have. Various types of rubber are cut to proportion and sent to the next stage of assembly. The wires are formed into rings and coated with rubber to make the beads, or seals, that will hold the tire to the wheel.

All the materials are brought to a worker using a special drum mount, who will assemble the tire itself.
All the materials are brought to a worker using a special drum mount, who will assemble the tire itself. The plies are wrapped around the drum in a certain pattern, almost always in the radial fashion these days, although certain specialty tires are still in the old bias-ply style. The plies are glued together, and the beads are fastened in place and covered with different plies to join them permanently to the tire. Then the sidewalls and treads are glued to the tire, and the new “green” tire is removed from the drum.
The green tire is then brought to a special mold which has a bladder inside. The tire is inserted over the bladder, the mold locked in place, and the bladder is filled with steam. The pressure forces the tire to expand, further fusing the rubber and pressing the tread rubber portion against the relief pattern around the inner edge of the mold. This will leave the bas-relief tread pattern as the tire tread on the new tire.
Time and temperature depend on the characteristics required for the tire, but, once removed, the tire is tested. This ensures that it has no major flaws and is balanced properly. Modern techniques mean that very few tires are rejected these days.

For example, none of these were rejected. That's pretty good; there's like twelve tires there.
So, how did we get here? Mostly trial and error, research and development, and a long process of innovation. Tire manufacturing started in the late 1800s, and was already a going concern by the time we pick up where we're interested, in the 1920s.
The first big innovation after that point was the introduction of steel wire as a component. Developed in 1934 by Michelin, already established as a major tire-maker at the time, the embedded steel wire allowed the bead to firmly attach the tire to the rim, invented in 1904. It quickly became industry standard, as did their radial tire developed in 1948.
Well, okay, industry standard in Europe, anyway. American car and tire manufacturers resisted it strongly, despite its various advantages. Let's see why.

Here they are, resisting in their old-timey way.
As mentioned, the plies in the bias-ply are laid on the tire at approximately 55-degrees. The part we concealed from you there, so we could reveal it here, is that the plies covered the entire tire, from bead to bead, across the sidewall and under the tread of the tire. Four plies under the tread meant that there were also the same four plies behind the sidewall.
Doesn't seem like such a big deal, right? Well, as you might have guessed from the very fact that we prompted you with that rhetorical question: yes. It meant more heat build-up in the tire at the expense of the strength. Buses and heavy trucks could have up to twenty plies in their tires, and the heat generated meant that they needed to replace those tires rapidly, as they were basically melting their treads off. Michelin - them again - developed steel cord plies in the late 1930s to retain the strength while lowering the number of plies needed, increasing the useful life of those tires.
So it went, until Michelin decided to research tire treads in the 1940s. They developed a special test tire that would show how the treads were acting in isolation, which is to say, without the sidewalls' interaction. To their surprise, they discovered that the treads were not to blame for heat failures. Rather, it was the sidewalls: the multiple plies inside were being flexed at opposing angles and generating friction-based heat at the molecular level. Clearly a problem.
They had to isolate the tire tread from the rest of the tire, while retaining the superior wear characteristics of the ply manufacture, without building in the sabotaging characteristics of that same manufacture. The answer was simple: Don't put plies in the sidewalls.
The test tire already had a design that allowed for that. A new prototype tire was designed that only had a single layer of cotton ply laid at 90-degrees to the edge of the tread, reinforced with a belt of the steel wires used in the heavy-duty plies going parallel to the tread. Early tests were extremely promising; in just a few years, Michelin had abandoned all bias-ply manufacture to produce only radial tires. Italian car manufacturers Lancia and Alfa Romeo had, by that point, already installed radials as factory equipment on their new car models.

Not technically the new one then, but it would definitely have had radials and looks awesome.
Sounds great! So why didn't the American car companies follow suit?
There are several advantages to the radial tire, but it has a few disadvantages compared to the bias-ply as well. First, the advantages: better heat distribution, as discussed above, which increased tread life; better control since the footprint is not limited by the inflexibility of the plies; and better gas mileage due to less rolling resistance.
The disadvantages: a somewhat harder ride (at least in the early days); a more complex construction which made them almost half again as expensive as a bias-ply; and the requirement for a different suspension system, which meant that they couldn't be installed on older models of cars, and that future car models would have to accommodate the new tires, necessitating revamping of existing manufacturing plants.

This is meant to look cross, what with the grille snarling at you, but the color is too happy. Sorry!
Detroit was concerned that the costs it would take to redesign the suspensions for all cars would be prohibitive. The tire manufacturers in America didn't like the idea of revamping all their factories to produce the new style of tire, so they all basically just decided to regard the new technology as a passing fad that they wouldn't need to worry about, and tried to forget about it.
Most of them tried, anyway. Goodrich invested very heavily in radial tires and even introduced its own version in 1965, which was ignored and eventually got Goodrich out of the tire industry for a time. Goodyear, on the other hand, opted to split the difference and, in 1967, designed a bias-belted tire that was essentially a bias-ply tire, just like always, with a fiberglass belt reinforcing it as the steel wire belt did on the radials.
Its tests showed it would last 30,000 miles, compared to the 20,000 for bias-ply and 40,000 for radials. A pretty good showing, especially as it dodged the two main concerns: It could be manufactured on bias-ply machines and mounted on cars that were designed to mount bias-ply tires.
A very good showing, actually, since that design went from two percent of the American factory-equipment market to almost ninety percent between 1968 and the early 1970s.
But, of course, in the early 1970s came the gasoline crisis. Gas jumped from thirty cents a gallon to over a dollar. Americans suddenly needed more economical cars and, would you look at that, the imports that they hadn't been buying were quite a bit more economical.
Sales of import cars went from fifteen percent of the market to almost thirty percent by the early 1980s. And all of those import cars came with radials as factory standard equipment. You may recall that radials improved gas mileage. Americans demanded radials, and overseas companies like Michelin and Pirelli were eager to help.

Firestone had a loss of 106,000,000…
Firestone, in the mid-1970s, decided to get in on the suddenly wide-open market for radials. Sure, makes sense, fine. Except they decided to save some capital by producing them on the same machines they used to make bias-ply tires. If you've been paying attention, you probably have a pretty good guess as to the next step in that procedure, which was to have to recall around nine million of those tires since they started to come apart with no real provocation other than “being on a car.”
The error almost destroyed the company, which went from a $110 million profit to a $106 million loss, with a 25,000 worker layoff. It only survived because Bridgestone bought them out in 1988.
Eventually, of course, the American tire industry and automobile manufacturers got swept along by the tides of history and, since 1983, all new American cars have factory equipped radial tires. So there's that.
The other major development in the evolution of the modern tire was the tubeless tire, which basically replaced the inner-tube version by the early 1960s, with the first factory standard tubeless tire coming equipped to the Packard in 1954.

Probably this exact one, actually; who can say
Which leads us to the modern era, with our tubeless radial tires and the advanced manufacturing techniques and whatnot. Surely this is the pinnacle of tire technology, right? There can be no greater heights to achieve! We challenge anyone to write and try to weave a tale of a new tire that …

… is magnetic and figures out the road conditions automatically!
Well, okay, then. What we meant to say was, bring on the future!